EMC’s Quality Team (They are kind of like the Loch Ness Monster)
October 20, 2020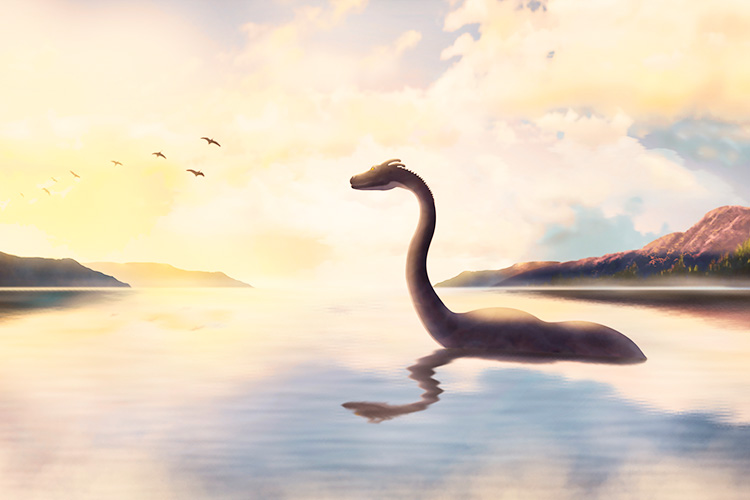
You may not be so sure that you’ve ever actually seen these guys, but they do exist. And, they travel...they travel A LOT.
So, while you may not be overly familiar with EMC’s Quality Team, they are familiar with many of your teams. They have likely visited several sites that your teams have worked on and it is likely that they have provided sage advice to your teams to help them realize success at a job site or two.
In some cases, they are the ones who have traveled back to sites to fix something that was not done to specification or to simply review the work just completed and to provide quality updates to our customers.
EMC’s Quality Team is constantly in motion in support of our project activity. So, they do exist, and they are eager to do more to help you.
The Quality Team: Introductions + Day 1 Tips
The Quality Team comprises three individuals. Here they are with their “End of Day 1” project tips:
![]() |
Gary Giesen: EMC employee since 2018 – master electrician – 31yrs in industry – safety specialist
|
![]() |
Bruce Brantford: EMC employee since 2021 – master electrician – 32yrs in industry
|
![]() |
Neil Giesen: EMC employee since 2019 – journeyman electrician – 16yrs in industry
|
Improving Access to our Quality Team
Expertise is only as valuable as it is available. So, we are working on improved access and earlier access to these team members for our labor partners. We know that not all our labor partners have worked with the materials that are a part of our projects, and sometimes new site types can be a challenge. The Quality Team is very familiar with the materials and the installation difficulties that our projects can present. Their insights and experience can help your teams avoid critical in-field issues.
Reach out…Please!
It is possible that if you call at 3 a.m., they may be asleep, but the Quality Team works to be available when an answer is needed. They know your schedules and prefer that you reach out to one of them to ask a key question rather than delay work or completion of a project, or worse yet, continue to install materials incorrectly, resulting in costly go-backs and customer complaints.
John Loheit is EMC's Director of Labor Partner Development. In this role he oversees the Labor Partner Network and Field Quality Assurance. He holds a bachelor’s degree from Augsburg College in Minneapolis, MN.