Go-backs (Yuck!)
January 31, 2024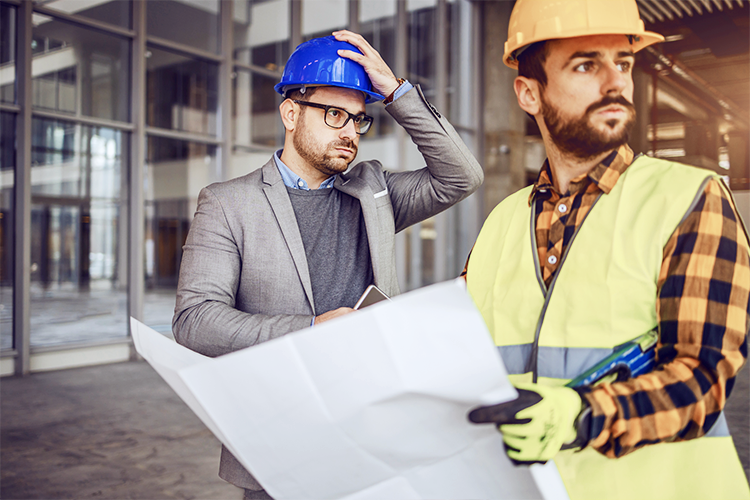
Everyone who enjoys working on go-backs, please stand up…
…that’s what I thought.
I have yet to meet anyone who likes the idea of a go-back.
The additional time and cost associated with managing and completing a go-back negatively impacts profitability and customer satisfaction for all concerned.
The value of a timely completion of the go-back can’t be overstated.
In some cases, a delay in completing these can lead to delayed awards from a customer, and delayed revenue for all parties.
Does this sound familiar?
The team has been busy pulling all the recycling material together, getting the trash out the back and readying to move on to the next site in the run, when one of your area leads runs up to you with some install count information and a few notes.
In the notes you see that there was an area that couldn’t be completed because of a damaged fixture.
When you ask about it, you hear that the crew was just too busy, and they couldn’t get your lead the information until final updates were being provided.
It’s clearly an install communication error.
A go-back...ARGH!
Or this…
The project stretched out a bit due to access issues within the facility. The customer had a hard time coordinating personnel and their spaces to allow your team the ability to get in and out as planned.
The last night has arrived, and the last pallet of material is off the truck and on its way to the last two work areas when you realize that the count of fixtures remaining and the count of fixtures in those remaining boxes doesn’t match.
An audit error.
A go-back...ARGH!
While there is certainly great value in addressing go-backs quickly, there are some things that can be done in the field to reduce the need for them.
Here are three things that can help in avoiding go-backs:
1. Material counts
While material loads can be difficult to count due to the sheer size of the storage containers, trucks, or areas where they are stored, counting is one of the most effective ways to avoid go-backs.
Material shortages happen. Knowing about the shortage early enough in the project allows the project manager and the material provider to work toward a quick delivery so the team can install the material before leaving the site.
Go-back avoided!
2. Site walk and scope review
A site-walk and scope review ensure all areas are accounted for in a plan. Accounting for each area of the project provides the team with early awareness of either spaces that may not have been captured or captured correctly, or areas that may have become an issue since the audit was completed.
Outages happen all the time, and it isn’t uncommon that an outage occurs between the time of the audit and the first night of project work. Completing a full site-walk and scope review on the first night can help identify issues so the team can work to resolve the issue before project completion.
Go-back avoided!
3. Prompt communication
A busy job site is common, but it can also cause important updates and information to be delayed in getting to the project manager for action that may be needed.
A quick call, email or text to the project manager allows all involved more time to react to the situation and find solutions before the last day of scheduled install activities.
Go-back avoided!
Conditions are never perfect, and our ability to put any of these situations into a nice, neat package isn’t going to be the case 100% of the time.
That said, if we pay closer attention to all the points within the process that can provide us with an advantage in the go-back game, then we may be able to win more often when working to complete projects during the first visit to the site.
I’m interested in your feedback: In your opinion, what is the largest single reason for go-backs? Take the LP Survey.
John Loheit is EMC's Director of Labor Partner Development. In this role he oversees the Labor Partner Network and Field Quality Assurance. He holds a bachelor’s degree from Augsburg College in Minneapolis, MN.