Measure Twice. Cut Once.
January 26, 2022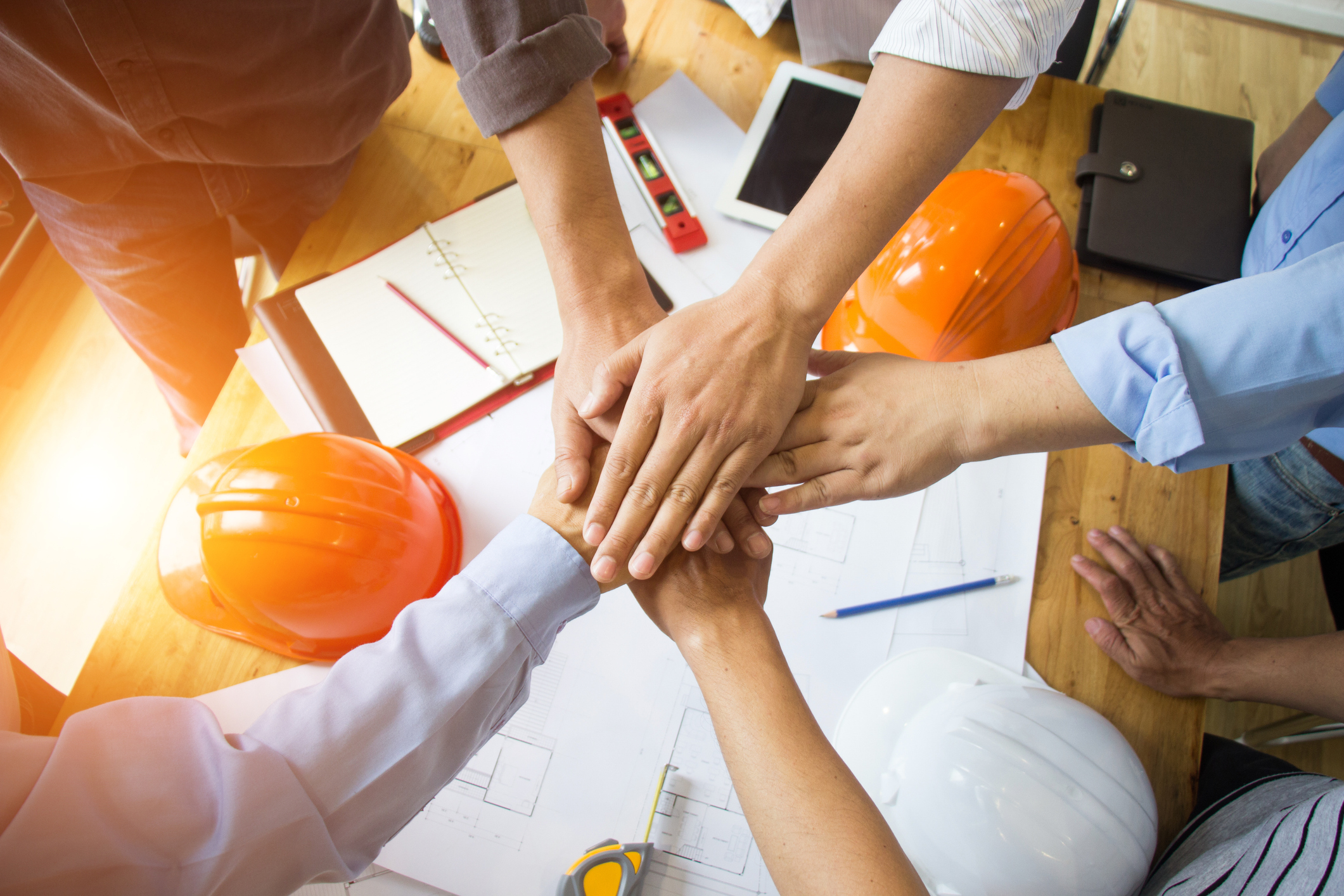
As any carpenter worth their salt will tell you, if you don’t do the job measuring, then a quality cut…well, it just ain’t gonna cut it.
We have been working to increase our process of measuring the work that is done through EMC’s labor partner network and we have also been working to measure and gain feedback on the efforts we’re making to support our labor partner network.
In October we hosted LPS21, a labor partner summit with a select group of EMC labor partners. The conversations were very good and the output from those talks has been reviewed by all participants to provide additional feedback concerning priorities.
Here are a few things we heard are priorities:
- Business and labor forecasting
- Material coordination and communication
- iSupplier ease of use
- Project folder checklists
- Escalation processes to resolve issues with EMC personnel
Participants noted a handful of other topics as well and we are reviewing all for next steps.
Some steps have already been taken based on feedback received, but more will be taken to continue to improve in each area.
We also announced at LPS21 that we would be launching LP project feedback surveys to continue to gather your thoughts about our performance during projects. Distribution of these surveys will begin with project completions after February 1. We look forward to your feedback.
Remember that the effort to improve is ongoing. With EMC’s core value of Continuously Improve + Driving Change, we understand that it takes effort to gather and react to information, data and feedback. This is not a process that has a beginning AND an end for anyone. When fully embraced, it has only a beginning.
As you look within your own business, you may find yourself wondering…Where would I start if I were going to try to improve my processes or my business?
Here are a couple of things to either avoid or more seriously question before pursuing:
- Why are you yelling? Oftentimes the loudest voice in the room (which can be in your own head) is focused on a short-term issue, usually something that is immediately in front of everyone as a pain point. The loud voice can easily distract you from making deeper, more meaningful changes to higher value issues. Acknowledge the loud voice (which can be done by making it a parking lot item) but take the time necessary to vet it out before unnecessarily spending your valuable time solving it. Focus on the high value issues, which are not necessarily the ones that everyone is yelling about.
- Where’s the data? An issue without something to support a direction for change will oftentimes result in a series of process improvement misfires. While data can lie to us and isn’t always readily available, there is no good reason we shouldn’t look for it. If there is none, make use of well-considered anecdotal information. Use it as a good starting point and then be sure to check as you go to confirm you are getting the desired results.
A couple of things to look for as areas of focus for improvements that could be valuable…
- Mystery costs. These added or phantom installation or material costs can creep into your operational reviews. If they are causing your margins to swing wildly or if they are typically associated with poor customer results, dig in to solve the mystery and improve your bottom line.
- Foggy bridges. Most organizations have multiple sub-teams with each team responsible for a piece of the process. Without clear hand-offs the process costs can add up in a hurry. Incomplete or poorly organized information or a lack of process definition can all lead to internal “go-backs” and an increase in the costs you bear to deliver. Clear the fog and cut your process costs.
Have process improvement stories to share?
I am always interested in process improvement efforts and how they have shaped organizations. If you have any stories to share about improvement efforts you have pursued, I am very interested to hear about them. Call me or email me if you have the time.
We will continue to seek input to improve what EMC is doing as a partner and we will continue to look inward to evaluate our own performance.
We welcome your feedback and look forward to working together in 2022 to improve results for our common customers.
And, remember to measure twice before cutting into a process to improve things.
John Loheit is EMC's Director of Labor Partner Development. In this role he oversees the Labor Partner Network and Field Quality Assurance. He has been in the lighting industry for 16 years, and holds a bachelor’s degree from Augsburg University in Minneapolis, MN.