Shedding Light on Reduced Operating Expenses
May 15, 2017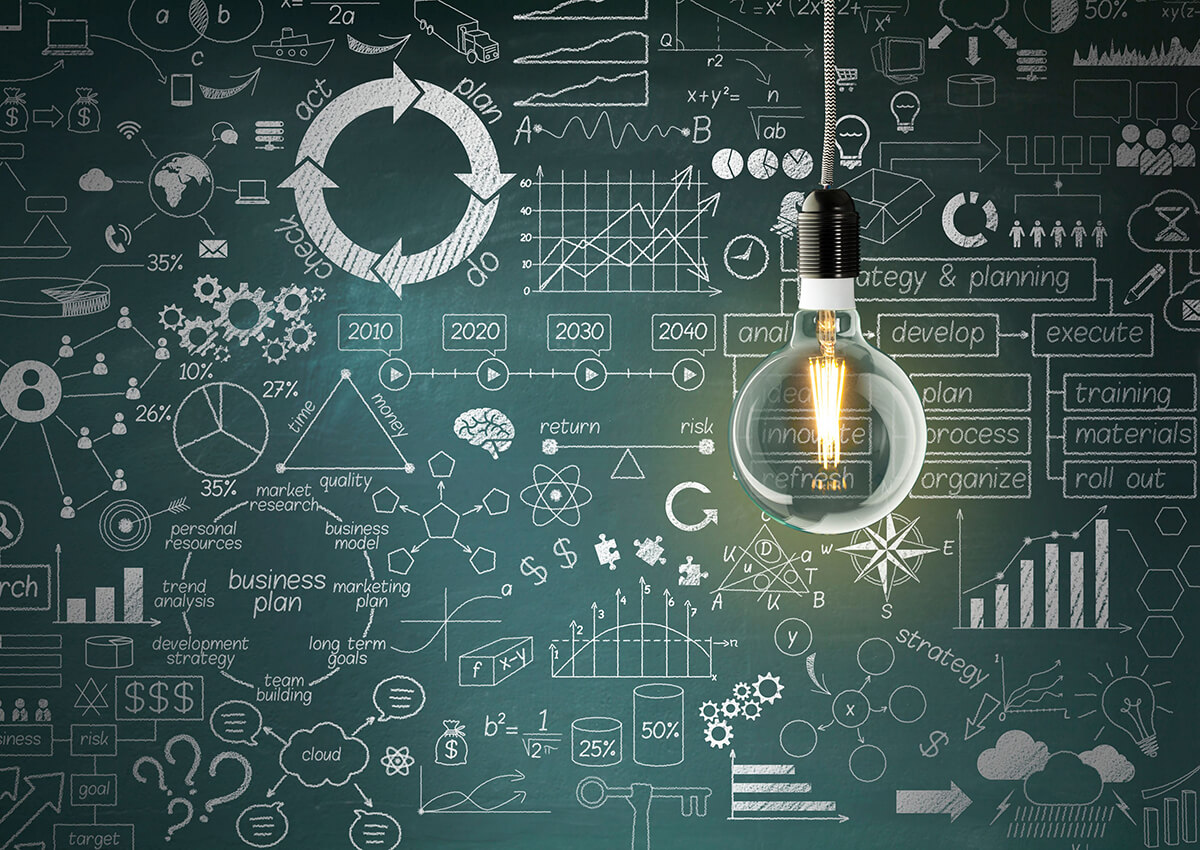
You think you’ve got your operating expenses as lean as they can get. But if you haven’t recently upgraded your facilities’ lighting to LED technology, you are missing out on some significant savings opportunities.
Often viewed as a fixed expense, updating lighting is one way to reduce your energy expenses by as much as 50 percent.
Energy efficient LED lights use 50 percent less energy than typical fluorescent bulbs. An added bonus is that LED lights also last up to 20 times longer than traditional bulbs, significantly reducing replacement costs and minimizing service calls.
Incredible advances in LED lighting technology continue to occur. Only eight percent of lighting sales were LED in 2012, but it is expected to reach 69 percent by 2020 and nearly 95 percent by 2025. In 2015 Goldman Sachs called out the LED industry as one of “the fastest technology shifts in human history.”
While these energy savings have an immediate impact on your bottom line, the retrofit process requires an upfront investment, a sound project plan and process management.
So how do you make the most of that investment? By being mindful about managing that upfront cost.
One way to do this is to be vendor neutral. We are fortunate that there are literally thousands of LED offerings from hundreds of manufacturers, giving you the flexibility to decide the factors that are the best fit for your operations. This allows you to prioritize important considerations like:
Lighting aesthetics. LEDs enable you to create dynamic lighting environments that use brightness, light distribution and color to create a certain mood and influence how people think and feel when they enter your environment.
Unlike fluorescents, LEDs come in a broad color range and are easily dimmable, so you can adjust the lighting to fit the time of day. Vendor neutrality allows you to pick the best product for each of your lighting needs. While it’s easy to look for one lighting vendor, you sacrifice that “best fit” solution for some or all of your lighting needs.
Product performance. The directionality of light matters and the change to small LED light sources makes it possible to shrink the optics, using small metal reflectors or small optical refractors to direct the light.
“Good lumens” fall in the areas we want to illuminate. Lighting products that maximize the amount of good lumens versus “bad lumens,” those that fall outside the intended area, often mean you are getting the most for your energy output. In essence, bad lumens are wasted energy—in the case of exterior parking lots, this is the light that shines upward or on grass versus the intended parking lot of your restaurant.
With an average life expectancy of 10 years, LED lighting significantly outperforms all other mainstream technologies.
Luckily, the Designlights Consortium, a partnership of lighting industry stakeholders dedicated to accelerating the widespread adoption of high-performing, energy efficient commercial lighting solutions, keeps a list of product offerings that meet specific quality and performance standards. Working with products on this list is a great way to make best-in-class choices for your lighting design.
Controls. Lighting controls create higher quality building environments and give you broader oversight of your energy use from lighting and other sources.
For instance, time based control systems allow lights to be automatically turned on and off via a timeclock or lighting control panel system. This ensures the last person to leave for the day does not have to remember to shut off lights and equipment. It can then turn lighting and systems on in the morning for those who open your facility.
Controls also help you take advantage of natural, ambient light. Sensors detecting daylight can adjust lights to the right level of brightness.
Like LED technology, controls technology is exploding and the industry is taking note. If you’ve been looking at opportunities to add lighting controls, now is the time to consider making the leap and further maximize your savings potential.
Utility incentives. When you pay your operations’ utility bills each month, you’re doing more than just keeping the lights on.
A portion of these dollars go toward efficiency programs in the form of custom and prescriptive energy efficiency rebates and incentives offered by hundreds of utilities across the nation. They can offset project costs and help you achieve bottom line savings faster during your next lighting retrofit project.
Rebates, which are a return of a portion of costs for service and/or merchandise, are ways utilities reward you for taking action as part of your normal business practices.
Incentives are used by utilities to elicit a change in behavior and an investment in efficiencies. It’s a way of driving new customer investment and behaviors to save energy through approved project elements.
Utility rebates and incentives become important because they can impact which locations you select for your lighting retrofit. Taking a vendor neutral approach builds on the savings as utilities often specify the types of lighting product you use in their programs. The savings utility incentives and rebates deliver help your project dollars go farther.
Payback
A lighting retrofit is a significant undertaking and can distract you from the important work you do to run your business. If it is up to you to select a lighting retrofit provider, choose one that makes vendor neutrality a cornerstone of its business. This organization should be well connected within the lighting industry and a utility trade ally. These qualities mean you have a skilled and knowledgeable resource for program guidelines and timelines and someone who will know how to deal with program changes that commonly occur during retrofit projects.
No matter whether your facilities are in one location or several spread across the country, lighting experts can help you understand how to optimize this equation:
Project Costs – Incentives
Energy Reduction (kW) x Operating Hours x Utility rate
Essentially you are taking your project costs and subtracting the utility incentive programs you are able to participate in for the project. Next, consider the energy reduction you are able to achieve and multiply it by the number of hours you operate and the utility rate. Divide the top number by the bottom. Do this for each location.
Knowing the components of this equation gives you clear insight into how you can prioritize your lighting project opportunities, make the most of your lighting project dollars and deliver the bottom line savings you need to stay competitive in this tough climate.
Tony Johnson is Energy Management Collaborative’s Customer Solutions Specialist. In this role he combines his background in lighting + controls design and solid state light fixture design with his expertise in energy savings to evaluate emerging technologies and solutions for EMC customers. He holds a Bachelor’s degree in architectural engineering from The University of Kansas.